Can you give an overview of the unique expertise and experience offered by Takumi Precision Engineering to highlight the key products and services you offer?
Takumi is a manufacturing engineering business that specialises in the production of high-quality precision components across a multitude of sectors. The majority of our business is focused on the Aerospace and Medical Device sectors. Our capabilities within these sectors are world-class. Very specific standards are required to be met in the manufacture of structural components for airplanes as well as the production of surgical and orthopaedic devices.
Founded in 1998, we have developed a strong and highly credible reputation over the years in both these worlds. We continue to upskill our employees and invest in the highest quality equipment and machinery available to enable us to continue to deliver best-in-class components to our customers.
How do Takumi Precision Engineering’s capabilities help differentiate it from competitors?
In order to stand apart from our competitors, the ethos in the heart and soul of Takumi lies firmly within our mindset, which is one of quality, innovation and constantly seeking to progress our ways of working with what we deliver for our customers. Our highly dedicated team remains at the centre of this, and the commitment from our employees to embrace change and evolve has proved over time to be a major factor in our growth and success.
Can you provide a couple of case study examples of unique products delivered to a client in the past year please Gerry?
The evolution of our digital processes has been one to which Takumi is committed across all aspects of the business.
How has Takumi Precision Engineering sought to use the latest technology through investment in your facilities, plant and staff in this most difficult of years?
The digital journey that Takumi has undertaken over the last number of years is truly something quite unique in the industry. We are very proud of how we have found huge efficiencies within the business through the integration and development of our ERP and IT systems.
Examples of this can be easily seen in all aspects of the business from Order Input, Inspection, Reporting, Purchasing, and Shipping right the way through to our payroll system. Labour-intensive activities such as data inputting have been automated, which allows us the opportunity to get through a higher volume of workload on any given day. Finding and driving efficiencies and working in a LEAN method increase our capabilities to deliver. Embracing Industry 4.0 and our digital journey has led us to continue to deliver higher output, making for a more efficient plant.
As the old saying goes, a bad workman blames his tools and we have neither in Takumi. We have significant resources invested in the continuous upskilling of our staff. Induction and training delivery from Team Leaders has been enhanced with the introduction of the creation of Training Videos. These videos are real Takumi life and maintain our standards whilst giving employees a truly identifiable education. They can physically see the machine they are working on, and the job cards they fill out.
Over the years Takumi has continuously invested in our machinery and will continue to do so. Our list of capital equipment continues to build and the use of robotics as we advance gives us the opportunity to have room for “lights-out” machining.
You operate across multiple sectors; can you shed a little light on which are keeping you busy at the present?
The initial stages of the Covid-19 pandemic sent more than a shiver down the spine the world over. As airplanes were grounded and businesses closed the skies looked more than empty. The Irish Government were quick to release a list of essential businesses that could remain operational during this time and Medical Device Manufacturers were key to this list. While we had no choice but to reduce the workforce in line with the reduction in Aerospace orders, we found there was an increase in demand from our Medical Device customers. For example, we manufacture tooling for PPE on medical-grade facemasks, a key element in the fight against the virus. There were many enquiries surrounding the production of components for ventilators and indeed we won new business during this period also for the production of a component for Corona testing machines.
As we passed through the phases of lockdown we began to see our Aerospace customers re-open. The resilience of this sector is consistently strong and while the order books were reduced, they did not close. We are back into our program of production for our biggest Aerospace customer with a healthy number of new enquiries continuing to come.
How does your supply chain support your ambitions and service standards?
On both sides of the supply chain in and out of Takumi, the systems that we have in place have always ensured we are well supported. Our delivery programs with our customers are well managed and overseen by excellent quality procedures. The digitalisation of processes between Quality Depts and Shipping ensures on-time delivery schedules are met. Our facility allows us to hold stocks of materials that support production schedules. We are not constrained in any way by our supply chain, which assists the relatively generous programs in place with our customers.
What goals/objectives have you personally set for Takumi Precision Engineering for the short and long term?
We have long had a strategy for trading through Brexit and certainly, the MedTech sector in the UK is an area we are keen to dive deeper into.
One of the goals that this pandemic has certainly amplified within Takumi is the need to diversify our offering, as it is vital that no one sector of our business exposes us as vulnerable. We do not want to have all our eggs in one metaphorical basket.
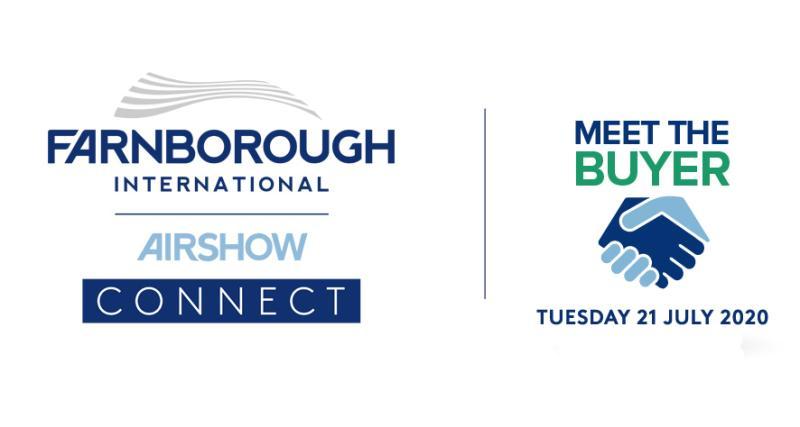